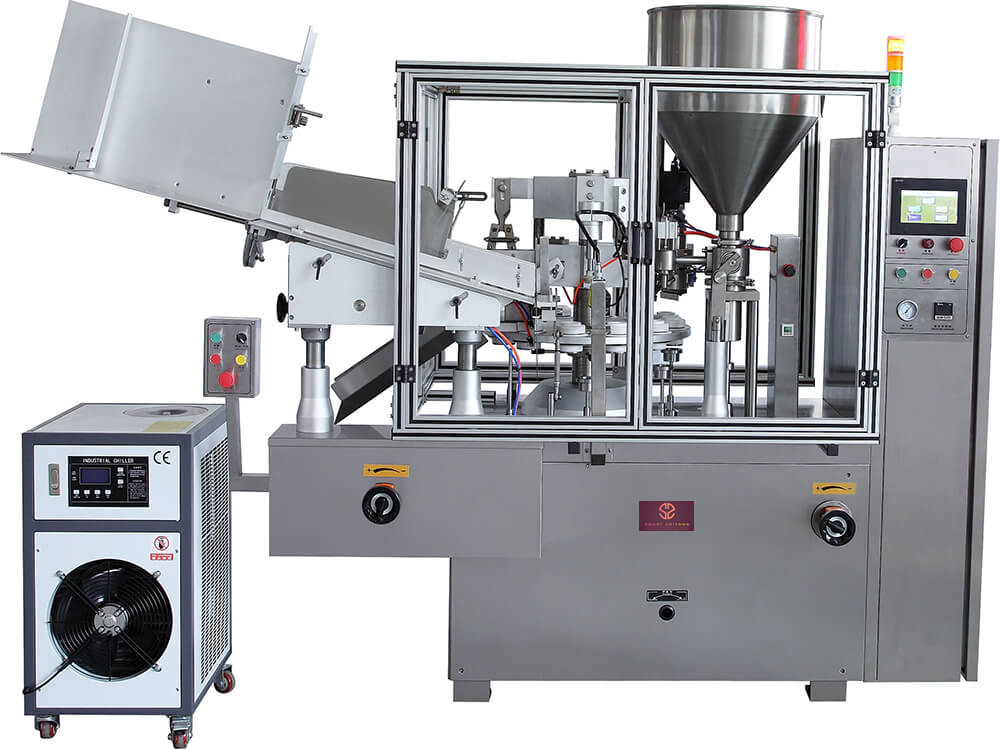
Automatic Filling and Sealing Machine operation, maintenance and maintenance procedures
Purpose: To establish a filling machine operation and maintenance procedures to standardize equipment and correct operation
Operation and maintenance and maintenance to ensure the integrity and good operation of the equipment.
Scope: Suitable for workshop filling machine operators, maintenance personnel. Responsibilities: Equipment Department, Production Department.
content:
1. Operating procedures forAutomatic Filling and Sealing Machine
1.1. Check whether all parts of Automatic Filling Sealing Machine are intact and firm, whether the power supply voltage is normal, and whether the gas circuit is normal.
1.2. Check whether the tube holder chain, cup holder, cam, switch and color code are in good condition and reliable.
1.3. Check whether the connection and lubrication of each mechanical part are in good condition.
1.4. Check whether the tube loading station of , tube crimping station, light alignment station, filling station, and tail sealing station are Coordinated.
1.5. Clear tools and other items around the equipment.
1.6. Check whether all parts of the feeding unit are intact and firm.
1.7. Check whether the control switch of Automatic Filling Sealing Machine is in the original position, and turn the machine with the hand wheel to determine whether there is any reason barrier.
1.8. After confirming that the previous process is normal, turn on the power and the air valve, and start the machine for trial operation.
Run at high speed, and gradually increase to normal speed after normal operation.
1.9. The upper tube station adjusts the speed of the upper tube motor to match the speed of the electric rod puller with the machine speed.
Keep the automatic drop tube running.
1.10. The pressure tube station drives the pressure head to move simultaneously through the up and down reciprocating motion of the cam linkage mechanism.
OK, press the hose into the correct position.
1.11. Use the hand wheel to move the car to the light position, turn the light cam to make the light cam close to the switch, and let the light beam of the photoelectric switch irradiate the center of the color mark, with a distance of 5-10 mm.
1.12. The filling station of Automatic Filling Sealing Machine is that when the tube is lifted at the light station, the tube lifts up the probe above the cone end
The signal of the proximity switch passes through the PLC and then through the solenoid valve to make it work, leaving the end of the hose
Filling and injecting paste is finished at 20MM.
1.13. To adjust the filling volume, first loosen the nuts, then turn the respective screw rods and move the position of the stroke arm slider, increase outwards, otherwise adjust inwards, and finally lock the nuts.
1.14. The sealing station adjusts the upper and lower positions of the sealing knife holder according to the needs of the pipe, and the gap between the sealing knives is about 0.2MM.
1.15. Turn on the power and air source, start the automatic operation system, and the filling and sealing machine enters automatic operation.
1.16 Automatic Tube Filler and Sealer is strictly forbidden for non-maintenance operators to adjust the setting parameters arbitrarily. If the setting is incorrect, the unit may not work normally, and the unit may be damaged in severe cases. If it is necessary to adjust during the application process, please do it when the unit stops running.
1.17. It is strictly forbidden to adjust the unit when the unit is running.
1.18. Shutdown Press the "Stop" button, and then turn off the power switch and air source switch.
1.19. Thoroughly clean the feeding unit and the filling and sealing machine unit.
1.20. Keep records of equipment operation status and routine maintenance.
2. Maintenance specification:
2.1. All lubricated parts should be filled with enough lubricant to prevent mechanical wear.
2.2. During operation, the operator should operate in a standardized manner, and is not allowed to touch the various components of the machine tool while it is running, so as to avoid personal injury accidents. If any abnormal sound is found, it should be shut down in time to check until the cause is found out, and the machine can be turned on again after the fault is eliminated.
2.3. The lubricator must be oiled before each start-up of production (including the feeding unit)
2.4. Drain the accumulated water of the pressure reducing valve (including the feeding unit) after shutting down after each production
2.5. Clean the inside and outside of the filling machine, and it is strictly forbidden to wash with hot water higher than 45°C to avoid damage
Various components during operation to avoid personal injury accidents. If any abnormal sound is found, it should be shut down in time to check until the cause is found out, and the machine can be turned on again after the fault is eliminated.
2.3. The lubricator must be oiled before each start-up of production (including the feeding unit)
2.4. Drain the accumulated water of the pressure reducing valve (including the feeding unit) after shutting down after each production
2.5. Clean the inside and outside of the filling machine, and it is strictly forbidden to wash with hot water higher than 45°C to avoid damage sealing ring.
2.6. After each production, clean the machine and turn off the main power switch or unplug the power plug.
2.7. Regularly check sensor sensitivity
2.8. Tighten all connections.
2.9. Check the electrical control circuit and the connections of the sensors and tighten them.
2.10. Check and test whether the motor, heating system, PLC, and frequency converter are normal, and perform a cleaning test
Check whether the coefficient parameters are normal situation of Automatic Tube Filler and Sealer
2.11. Check whether the pneumatic and transmission mechanisms are in good condition, and make adjustments and add lubricating oil.
2.12. Equipment maintenance items of Automatic Tube Filler and Sealer are handled by the operator and maintenance records are kept.
ZT has many years of experience in the development, design Automatic Filling and Sealing Machine and Automatic Tube Filler and Sealer If you have concerns please contact
Website: https://www.cosmeticagitator.com/tubes-filling-machine/
Post time: Feb-06-2023